Dive Into the Globe of Light Weight Aluminum Casting: Understanding the Different Approaches
Light weight aluminum casting is a basic process in the production sector, with various approaches employed to produce precise and complex parts. From the conventional sand spreading method to the sophisticated die spreading process, each technique supplies distinct benefits depending on the needs of the project.
Sand Casting Approach
Sand casting, a widely-used technique in aluminum casting processes, involves creating mold and mildews made of compacted sand for putting liquified metal. When the mold is ready, it is safely positioned in a flask and molten light weight aluminum is poured into the cavity.
After the steel has cooled and solidified, the sand mold and mildew is escaped to expose the aluminum spreading. Sand spreading enables for the production of complex forms and huge components that might be hard or costly to produce utilizing other methods. It is additionally a lasting technique as the sand can be reused and utilized multiple times, reducing waste in the spreading process.
Permanent Mold And Mildew Strategy
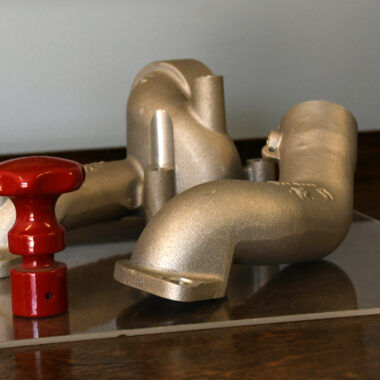
One significant advantage of the Permanent Mold Technique is the improved dimensional precision it offers. The steel mold and mildew permits for tighter resistances and better information in the last light weight aluminum spreadings compared to sand casting methods. This precision makes it a favored option for applications where tight dimensional control is essential, such as in the automobile and aerospace markets.
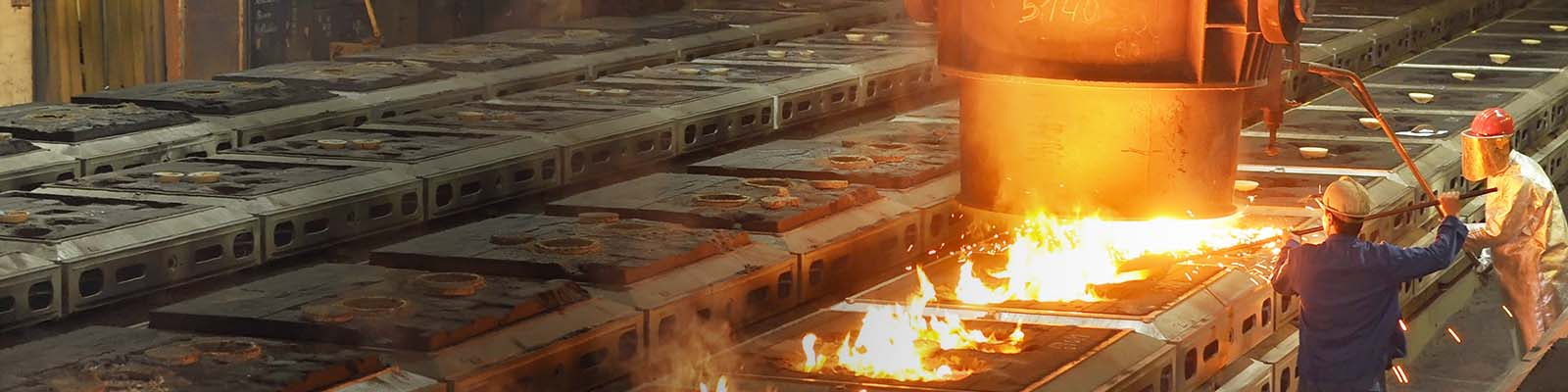
Die Casting Refine
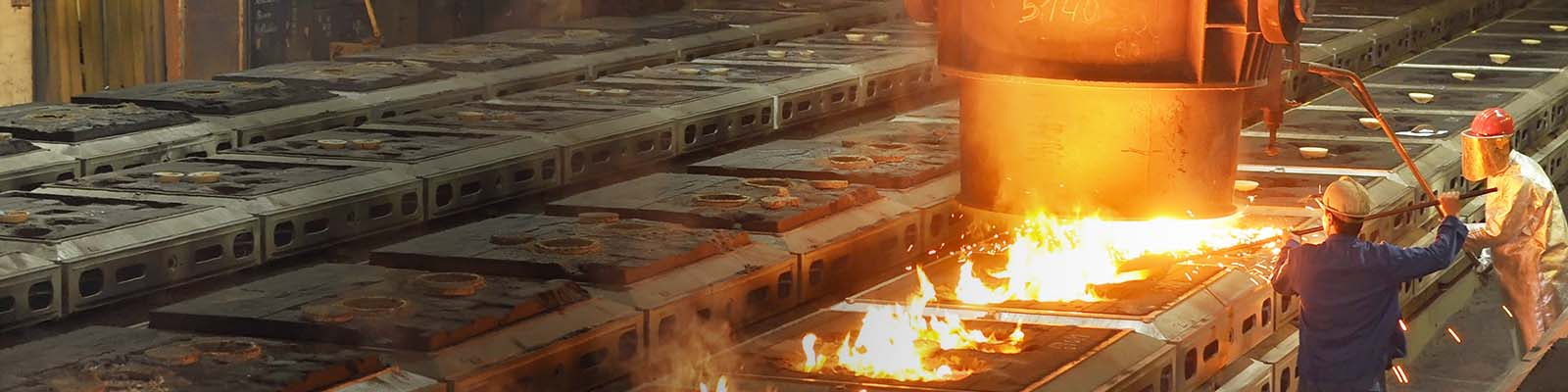
Investment Casting Approach
Using a precision spreading approach, Financial investment Casting Strategy includes creating intricate light weight aluminum elements by putting molten metal right into a ceramic mold. This procedure, likewise known as lost-wax casting, begins with the production of a wax pattern of the preferred part (aluminum casting).
The following step entails putting the molten aluminum right into the ceramic mold. The light weight aluminum fills the dental caries left by the wax pattern, taking its form exactly. This method is preferred for its ability to generate complex shapes with high precision and a smooth surface area coating. Investment spreading is typically made use of for manufacturing parts in industries where detailed designs and limited tolerances are called for, such as aerospace, automobile, and clinical equipment. The flexibility and accuracy of the Investment Casting Technique make it a valuable method worldwide of aluminum spreading.
Lost Foam Casting Approach
Having actually explored the elaborate precision of Investment Casting Technique, the focus now moves to the ingenious technique of Lost Foam Spreading in light weight aluminum part manufacturing. Lost Foam Spreading, additionally referred to as evaporative pattern spreading, Web Site is a modern-day strategy where a foam pattern of the desired component is produced and after that covered with a refractory product. The covered foam pattern is then buried in sand, and molten light weight aluminum is put right into the mold. As the metal fills the mold, the foam evaporates because of the warm, leaving a clean cavity in the shape of the desired component.
One of the main benefits of Lost Foam Spreading is its ability to create complex forms with detailed information, typically in a single piece without the demand for extra machining. This method you can try this out is also recognized for its high dimensional accuracy and smooth surface finish. In Addition, Lost Foam Casting is a cost-effective procedure as it minimizes the need for cores and permits the manufacturing of lightweight components. Regardless of its advantages, Lost Foam Spreading requires careful control of the spreading process to make certain and avoid issues quality parts.
Final Thought
Finally, light weight aluminum casting uses a selection of methods such as sand spreading, irreversible mold and mildew technique, die spreading, investment casting, and lost foam spreading. Each technique has its very own advantages and applications, making aluminum casting a flexible and extensively used process in various markets. Comprehending the distinctions in between these methods is important in picking one anchor of the most suitable casting method for certain manufacturing needs.
Sand spreading, a widely-used approach in light weight aluminum spreading processes, involves creating molds made of compacted sand for pouring molten metal. aluminum casting.The Permanent Mold Method, like sand casting, is one more prevalent method utilized in aluminum casting processes, offering distinctive advantages in terms of mold reusability and dimensional precision. The steel mold and mildew permits for tighter resistances and better details in the final light weight aluminum spreadings contrasted to sand spreading techniques. The 2 main kinds of die spreading are cool chamber pass away casting and hot chamber die spreading, each appropriate for different types of light weight aluminum alloys.In verdict, light weight aluminum casting offers a range of techniques such as sand casting, irreversible mold and mildew strategy, pass away casting, investment spreading, and shed foam casting